R.B. Arthur Technical Center
Articles
The R. B. Arthur Technical Center was formally dedicated on October 22, 2018. The technical center will serve as the Research and Development Laboratory for Resco Products, as well as a technical training center. As a Training Center, Resco will be able to provide classroom and hands-on training in the use and installation of refractory materials.
R.B. Arthur started working at the Greensboro facility (North State Pyrophyllite at the time) in 1954 during summers while he was in High School. He Graduated from North Carolina State University in 1959. After Graduating, R.B. continued to work in various positions from the laboratory to operations. In 1976 North State Pyrophyllite became part of Resco Products. R.B. became vice president of operations for Resco Products and was part of the Ownership group that led Resco starting in 1998. Upon his retirement as Vice President, R.B. continues to work as a consultant and provides leadership in the Cartop and Cordierite production.
His knowledge of the formulations and manufacturing of these product lines continues to make Resco highly successful in these areas. He has been a critical part of our coke oven sales efforts and has provided technical support in this area as well. R.B. has been part of Resco for over 64 years and continues to provide technical leadership and is now training the latest generation of engineers to continue his legacy. In honor of all the R.B has done to lead Resco to success, the new Technical Center has been named in his honor. R.B. Arthur's first day in 1954.
Technical Center Equipment and Capabilities
Raw Materials Crushing & Sizing
Our updated technical center has the capacity to crush and size up to a few hundred pounds of raw material for research and evaluation purposes. This allows us to
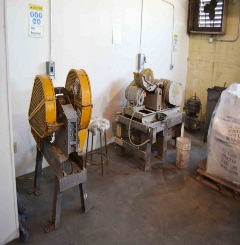
evaluate new raw materials sources. With the screening capabilities, both by down and split fractions can be produced. The following equipment is available.
- Chipmunk Jaw Crusher
- Roll Crusher
- Sweco Screen
- Jar Mills (Lab Scale Ball Mills)
- Ro-Taps and a complete set of testing Sieves
Batching & Blending
The new facility maintains a consistent supply of raw materials to test batches for product development and post mortem results of all products utilized by all Resco Product locations. The batching equipment includes various scales with capabilities to weight bulk materials as well as precise additive addition. Climate controlled storage of raw materials is available when needed. When blending mixes, the Technical Center has a variety of planetary (Hobart) mixers sizing from 5 quarts to 80 quarts and a lab scale Erich Mixer. With these mixers, the center can mix batches from about 2 to 200 lbs.
Flow & Consistency Testing
When testing castable materials the flow can be measured using tap, vibration, and self-flow methods. The type of testing done depends on the intended installation method of the material. This testing ensures that casting grade materials will install with consistent characteristics. The workability Index of Plastics and Ramming mixes is measured using a Sand Rammer. Mortar consistency can be measured by dart, precision penetrometer, and Vicat needle apparatus.
Sample Preparation
The technical Center can prepare monolithic samples by casting. Samples up to about 200 pounds can be vibration cast using the laboratory vibration table. A variety of molds are available to cast samples to size for a variety of standard test methods. This includes standard shapes for Cold Crush, MOR, and erosion testing, as well as specialized test such a thermal conductivity and cup test.
The tech center has a laboratory brick Press. This allows the research group to form pressed brick samples for testing. The dies can be changed in the press to form different shapes as needed. There is also a small-scale extruder. The 1.25” square extruder die allows the tech center to evaluate and development mixes for the cartop and other extrusion lines. An amp meter on the extruder gives the means to measure the extrudability of a mix.
Kiln Room
The technical center has a variety of electric kilns giving the ability to fire samples to temperatures up to 3100 degrees F. The Hot MOR furnace is capable of firing to 2700 F and performing Hot Modulus and Hot Load testing. There is a thermal conductivity kiln capable of running hot wire thermal conductivity up to 2500F. In addition to normal firing the following are some of the tests that can be run.
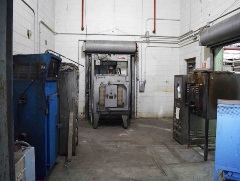
- HMOR
- Hot Load
- Aluminum cup Test
- Aluminum emersion test
- Thermal Shock
- Prism Spall
- Thermal conductivity by Hot Wire
- LOI
Physical Properties
The Technical center in conjunction with the QA laboratory has the ability to measure the standard physical properties of refractories using ASTM based testing methods. Some of the tests that can be performed include
• Cold Crush Strength
• Modulus of Rupture
• Erosion Loss (ASTM C-704)
• Permanent Linear Change
• Density
• Porosity
• Static Youngs Modulus
Environmental Chamber
The environmental chamber allows installation conditions of temperature and humidity to be duplicated in the lab. Used primary for castable, the environmental chamber lets us study the effects of ambient temperature and humidity on the curing and physical properties of castable. This capability has allowed the development of formulations designed for specific installation conditions. It can be used with the Sonic Set Time test.
Sonic Set Time
The sonic set time is a method for measuring the set time of monolithic refractories. The method measures the speed of sound through a small sample. As the sample sets and develops strength the speed of sound increases. By looking at the change in sound velocity over time, the working and setting time of the material can be measured. Unlike the exothermic test, this method does not require the bonding system to generate heat during curing to measure the set time. This allows us to measure Monolithics with a variety of bonding systems, that cannot be measured using exothermic testing. By combining the Sonic set Time test with the environmental chamber, setting characteristics can be measured at any ambient condition likely to be encountered on the job site.
Particle Size Characterization
The tech Center can measure the particle size of both finished goods and raw materials. The lab maintains a complete collection of laboratory sieves to perform wet and dry screen analysis using Ro-tap sieve shakers. To better evaluate the size distribution of fine particles, the Tech Center has a Cilas 1064 particle size analyzer. This device uses laser scattering to measure particle diameters down to 0.4 microns. Optical microscopes are available to examine particle shape.
Dry Gunnite
The technical center includes a covered gunnite test area, that is protected from the weather. This gives the lab the ability to test dry gunnite materials regardless of outside weather conditions. The lab uses a Reed SOVA gun for evaluating materials and test both sidewall and overhead gunning. Sample baskets can be gunned to perform physical properties testing. Once gunned samples are cut and fired as needed for physical properties testing.
Extended Testing Capabilities
The technical center has arrangements with a variety of corporate and university laboratories to extend the testing capabilities to include those that are performed in-house. These tests include Chemistry and XRD. Other testing can be performed as required and we are constantly upgrading our testing capabilities.