Resources
Articles
Rotary Kiln Discharge Zone Refractory Challenges
Part 1: Charging Zone
Part 2: Calcining Zone
Part 3: Burning Zone
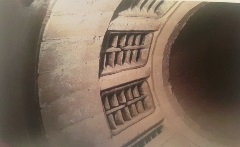
Discharge Zone Refractory Challenges
The discharge zone almost always includes a refractory dam construction. Brick refractory dams consist of concentric rings of brick and service to increase the residence time of the lime charge in the kiln. Dams can increase production and improve the quality of the lime product by achieving a more even degree of burn between the coarse and the fine particles in the charge.
Castable refractories can be used in the discharge end also, including dam constructions. As rotary kilns age, the steel shell in the discharge area can weaken and deform, causing brick constructions, including dams, to become unstable and loosen. Limekilns, especially in the paper industry, can use more complex constructions to incorporate grates or ports for planetary coolers (figure 6). Refractory construction in both conditions is facilitated by using monolithic refractories.
Damn constructions can have great lining thickness at their peaks, and this presents difficulties in the initial heating and dry-out of the monolithic refractory. QUIKTURN castable and gunning mixes have been developed for such difficult to dry-out applications. Most low-cement castable uses increased permeability to reduce the incidence of steam-spalling during dry out. QUIKTURN castable incorporates several other technologies to reduce dry-out time, in some cases to a quarter of the time required for a conventional low-cement castable. These advanced materials reduce the risk and expedite the initial heating of thick monolithic constructions
Rotary Kiln Refractory Challenges Conclusion
Refractory placement in the rotary pebble lime kiln requires an assessment of the conditions of service and the method of installation. Abrasion resistance is the prime consideration for the charging zone because of the abrasive nature of the stone feed, especially in long kilns that do not have preheaters. For the most severe conditions of abrasion, 80% alumina phosphate-bonded brick extends refractory life. Special extreme abrasion-resistant castable is available to be used in place of brick construction where brick installation would be too lengthy or difficult. Additionally, monolithic refractories are anchored to the steel shell, reducing the risk of lining looseness in difficult brick constructions.
In the calcining zone, 70% alumina refractory bricks are widely used. The calcining zone may also contain various kiln internals to promote heat transfer. Advancements in castable technology have made it possible to fabricate lifters and cross-type heat exchangers that provide good longevity of service.
High kiln shell temperatures in the burning zone challenge operators. The selection of magnesite-spinel brick with a consideration of the insulating value (low thermal conductivity) can help manage the hot kiln shells. Thicker brick linings in the burning zone provide better stability than two-layer refractory constructions and help to further reduce shell temperatures.
Dam construction is the discharge zone that can be either brick or monolithic. Specially formulated castable refractories call QUIKTURN™ meet the challenges of thermal shock resistance, and moderate abrasion resistance and stability for the dam construction, while reducing the risk of any difficulty in the initial dry-out of a very thick construction.
Written by: Christopher Macey - Resco Products Inc
Leave a comment

